What Is Soldering Flux?
The soldering flux is a chemical substance that helps and facilitates the soldering process, while having a protective effect and preventing oxidation reactions.
Flux is widely used in the brazing of watch and clock instruments, precision parts, medical devices, stainless steel crafts, tableware, mobile communications, digital products, air conditioning and refrigerator refrigeration equipment, eyeglasses, knives, automotive radiators and various PCB boards and BGA solder balls.
Function of Flux
Removal of surface oxides
Because of atmospheric oxygen, various substances are actually surrounded by a layer of oxide, the thickness of about 2 × 10-9 ~ 2 × 10-8 m. In welding, the oxide film will certainly prevent the solder to the wetting of the base material, welding can not be carried out properly, so must be coated with flux on the surface of the base material, so that the oxide on the surface of the base material to restore, so as to achieve the purpose of eliminating the oxide film.
On the other hand, the high temperature of welding tends to oxidize the surface of the welded material. Flux helps to stop the oxidation process.
Reduce the surface tension of the material
Surface tension of the material will affect the quality of welding, another role of flux to reduce the tension of the material. The surface tension of the molten solder will prevent it from diffusing to the surface of the base material, which affects the proper wetting process. When the flux covers the surface of the molten solder, the surface tension of the liquid solder can be reduced, so that the wetting performance is significantly improved.
Protect the base material of welding
The soldered material has destroyed the original surface protection layer during the welding process. Good flux after welding, and quickly return to the role of protecting the solder material. In addition, it can also accelerate the transfer of heat from the soldering iron tip to the solder and the surface of the solder, the right flux can also make the solder joint beautiful.
Features of Flux
Flux is an indispensable auxiliary material in the SMT soldering process. In wave soldering, flux and solder are used separately, while in reflow soldering, flux is used as an important part of solder paste. Soldering effect is good or bad, in addition to the quality of the welding process, components and PCBs, the choice of flux is very important. Good performance of the flux should have the following characteristics:
- Lower melting point than the solder, before the solder melts, the flux should be melted first, in order to give full play to the flux.
- infiltration and diffusion faster than the melted solder, usually requires expansion at about 90% or more than 90%.
- Viscosity and specific gravity than the solder is small, viscosity will make the infiltration diffusion difficult, the ratio is large can not cover the surface of the solder.
- Welding does not produce welding bead spatter, and does not produce toxic gas and strong irritating odor.
- After welding residue is easy to remove, and has no corrosion, non-hygroscopic and non-conductive properties.
- Non-stick, non-stick hands after welding, welding joints are not easy to pull the tip.
- Stable storage at room temperature.
Flux Types
There are four main types of fluxes: rosin (RO), resin (RE), organic (OR), and inorganic (IN). Each type of flux has 3 activity levels to choose from (low, medium and high.) The L, M and H levels are subdivided into two categories: halide-containing or non-halide-containing.
Rosin flux
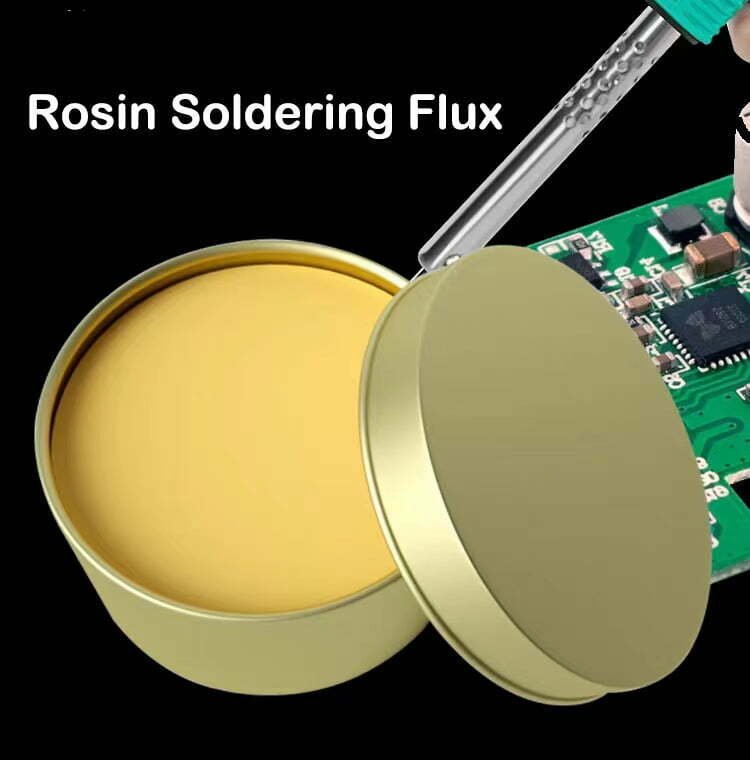
Rosin flux, also known as rosin soldering flux or soldering rosin. It helps remove oxides and other contaminants from the surface, allowing for better solder flow and stronger solder joints. Rosin flux is commonly used in both manual soldering and automated soldering processes.
Rosin flux is available in various forms, including liquid, paste, and solid (flux-cored solder wire). It is often applied using a soldering iron, soldering gun, or flux pen. The flux residue left after soldering should be cleaned to prevent any potential long-term corrosion or electrical issues.
Resin flux
The largest proportion of soldering in electronic products is used in resin flux. Because it can only be dissolved in organic solvents, it is also known as organic solvent flux, the main component is rosin. Rosin in the solid state is inactive, only when the liquid state is active, its melting point of 127 ℃ activity can last until 315 ℃. The best temperature of tin soldering is 240 ~ 250 ℃, so it is in the active temperature range of rosin, and its welding residues do not have corrosion problems, these characteristics make rosin for non-corrosive flux and is widely used in the welding of electronic equipment.
Organic flux
Organic series fluxes are between inorganic series fluxes and resin series fluxes, which also belong to acidic, water-soluble fluxes. Water-soluble flux containing organic acid based on lactic acid and citric acid, as its solder residue can be retained on the solder for a period of time without serious corrosion, so it can be used in the assembly of electronic devices, but generally not used in the SMT solder paste, because it does not have the viscosity of rosin flux (to play a role in preventing the movement of SMD components).
Inorganic flux
Inorganic series fluxes have strong chemical effects, fluxing performance is very good, but the corrosion effect is large, belonging to the acidic flux. Because it dissolves in water, it is also known as water-soluble flux, which includes inorganic acids and inorganic salts 2 types.
The main components of fluxes containing inorganic acids are hydrochloric acid, hydrofluoric acid, etc. The main components of fluxes containing inorganic salts are zinc chloride, ammonium chloride, etc. They must be cleaned very strictly immediately after use, because any residual halides on the soldered parts can cause serious corrosion. This flux is usually only used for non-electronic products soldering, in electronic equipment in the assembly of such inorganic series of flux is strictly prohibited.
How to Use Soldering Flux?
First, wipe the solder joint clean, apply a little humongous solder paste, then use the soldering iron to apply some solder, pinch the wire or pin to press on the solder joint, use the tip of the soldering iron to gently press on the solder joint to let enough tin flow to the solder joint after quickly taking the iron away, the soldering iron away and wait for the tin to cool and fix before releasing the pinch.
Instructions for use and preservation:
- The sealed storage period is six months, please do not freeze to store the product. The best storage temperature: 18 ℃ -25 ℃, the best storage humidity: 75% -85%.
- After long-term storage of flux, its specific gravity should be measured before use and adjusted to normal by adding diluent.
- The amount of flux coating depends on the needs of the product. The recommended amount of flux for single panel is 25-55ml/min, and the recommended amount of flux for double panel is 35-65ml/min.
- Flux preheating temperature, single panel board bottom recommended temperature: 75-105 ℃ (single panel board surface recommended temperature: 60-90 ℃), double panel board bottom recommended temperature: 85-120 ℃ (double panel board surface recommended temperature: 70-95 ℃).
- Solvent flux is a flammable chemical material, should be operated in a well-ventilated environment, and away from fire, avoid direct sunlight.
- When using flux in sealed cans, pay attention to the performance of the wave crest furnace and the characteristics of the product to reasonably adjust the spray volume and spray air pressure.
- When flux is used for a long time, a small amount of sediment will accumulate at the bottom of the sealed tank, which may lead to clogging of the spraying system of the wave oven. To avoid this problem, it is recommended to clean the spray system every week and replace the flux with precipitates.
How to Choose the Flux?
Flux with suitable melting point
In order to match the use of brazing material, the melting point of the selected flux should be lower than the melting point of brazing material 10-30 ℃. Flux melting point such as too lower than the melting point of the brazing material, it is easy to melt too early and lead to premature failure of the flux active ingredients.
Acidic or alkaline flux
For the alkaline oxide film, the acidic flux should be selected; and for the acidic oxide film, the alkaline flux should be selected.
Liquid, paste, or powder fluxes
According to the specific process to choose different forms of flux, such as wave soldering to choose liquid flux, high frequency or medium frequency induction brazing to choose paste flux, flame brazing to choose powder flux or paste flux, etc.
Active flux
Different substrate materials due to the different surface oxide film, the choice of flux type also exists a large difference, especially some difficult to weld metal, such as magnesium aluminum alloy, stainless steel, carbide, etc.. In order to ensure the welding performance of magnesium-aluminum alloy, usually choose a more active flux.