Printed circuit boards (PCBs) are the backbone of modern electronics. Ensuring their quality and performance is crucial.
This is where IPC 6011 comes into play. It sets the standard for PCB performance and quality.
IPC 6011 is a key document in the electronics industry. It provides guidelines for various PCB applications.
Understanding IPC 6011 is essential for professionals in electronics manufacturing. It helps ensure consistency and reliability.
The standard outlines different classes of PCBs. Each class has specific quality and performance criteria.
In this article, we will explore IPC 6011 in detail. We will also compare it with related standards like IPC 6012.
What is IPC 6011? An Overview
IPC 6011 is a critical standard in the world of electronics. It focuses on the performance and quality of printed circuit boards (PCBs).
This standard provides a general overview of requirements for PCBs. It is used in various electronic applications, ensuring they meet quality benchmarks.
As part of a series of standards, IPC 6011 lays the groundwork. It serves as a foundational document for other related standards.
Key aspects of IPC 6011 include:
- Establishing criteria for PCB classes.
- Outlining visual and electrical testing requirements.
- Emphasizing documentation and traceability.
The standard’s classifications ensure each PCB meets the specific needs of its intended use. These classes reflect the varied demands for reliability and quality.
IPC 6011 is globally recognized. This makes it essential for manufacturers who operate on an international scale, ensuring consistent quality across borders.
The standard not only sets benchmarks but also fosters innovation. By creating a common language, it allows for clearer communication between manufacturers and clients.
Understanding IPC 6011 is invaluable for those involved in PCB design and manufacturing. Its guidelines support effective quality assurance processes.
An image representation of a PCB under inspection:
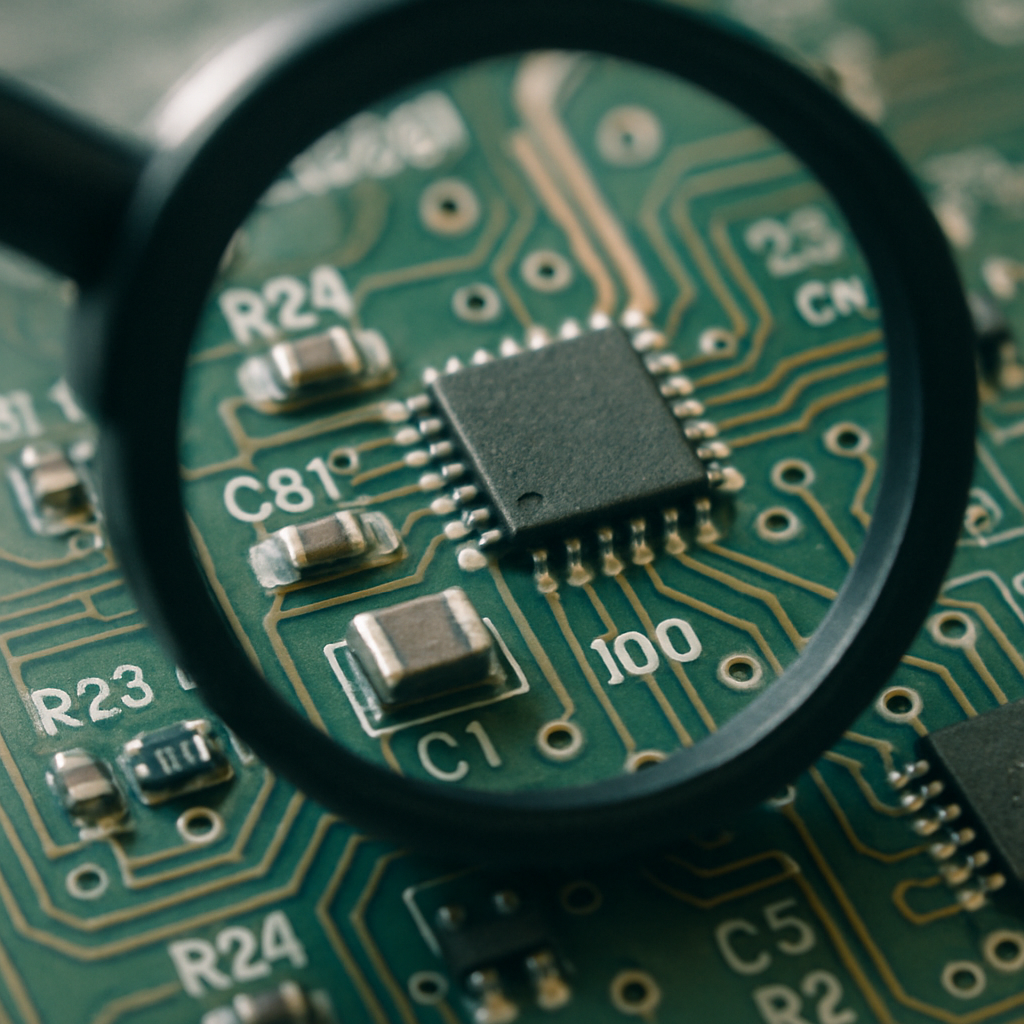
The Role of IPC 6011 in PCB Manufacturing
IPC 6011 plays a pivotal role in PCB manufacturing. It ensures PCBs meet quality expectations, which are vital in the electronics industry.
The standard supports manufacturers in maintaining consistent production practices. By following IPC 6011, companies can reduce defects, thus lowering costs associated with rework.
Manufacturers rely on IPC 6011 as a blueprint for quality assurance. This includes requirements for visual inspections and testing methods to verify product reliability.
Benefits of following IPC 6011 in manufacturing include:
- Enhanced product reliability and performance.
- Consistent quality and reduced variability.
- Improved customer satisfaction and trust.
The detailed guidelines in IPC 6011 help streamline manufacturing processes. It provides clear instructions for material selection and ensures that documentation supports traceability.
IPC 6011 also has a positive impact on global collaboration. By aligning with international standards, it facilitates trade and partnerships.
An image illustrating the stages of PCB manufacturing:
IPC 6011 Classifications: Class 1, Class 2, and Class 3 Explained
IPC 6011 categorizes PCBs into three classes based on their intended use and reliability. Each class serves different applications, ensuring tailored quality standards.
Class 1 is designated for general electronic products. These products have low reliability requirements and are often used in consumer electronics.
Key attributes of IPC 6011 Class 1 include:
- Basic performance requirements.
- Minimal reliability emphasis.
- Suitable for standard consumer goods.
Class 2 is intended for dedicated service electronic products. These products require higher performance and longer lifespan. They are typical in communications and instruments.
Class 2 characteristics:
- Enhanced reliability compared to Class 1.
- Balanced between cost and performance.
- Ideal for applications demanding stability.
Class 3 is used for high-reliability electronic products. Such products must consistently perform under critical conditions, like in aerospace or medical fields.
Features of Class 3 include:
- Stringent reliability and performance standards.
- Designed for critical and high-risk environments.
- Focused on durability and longevity.
Understanding these classifications helps in selecting the correct PCB quality level for specific applications.
This classification system allows designers and manufacturers to choose appropriate standards. They match the demands and conditions of their product’s use.
Comprehending the differences among these classes is crucial for engineers. It ensures they make informed decisions during PCB design and manufacturing.
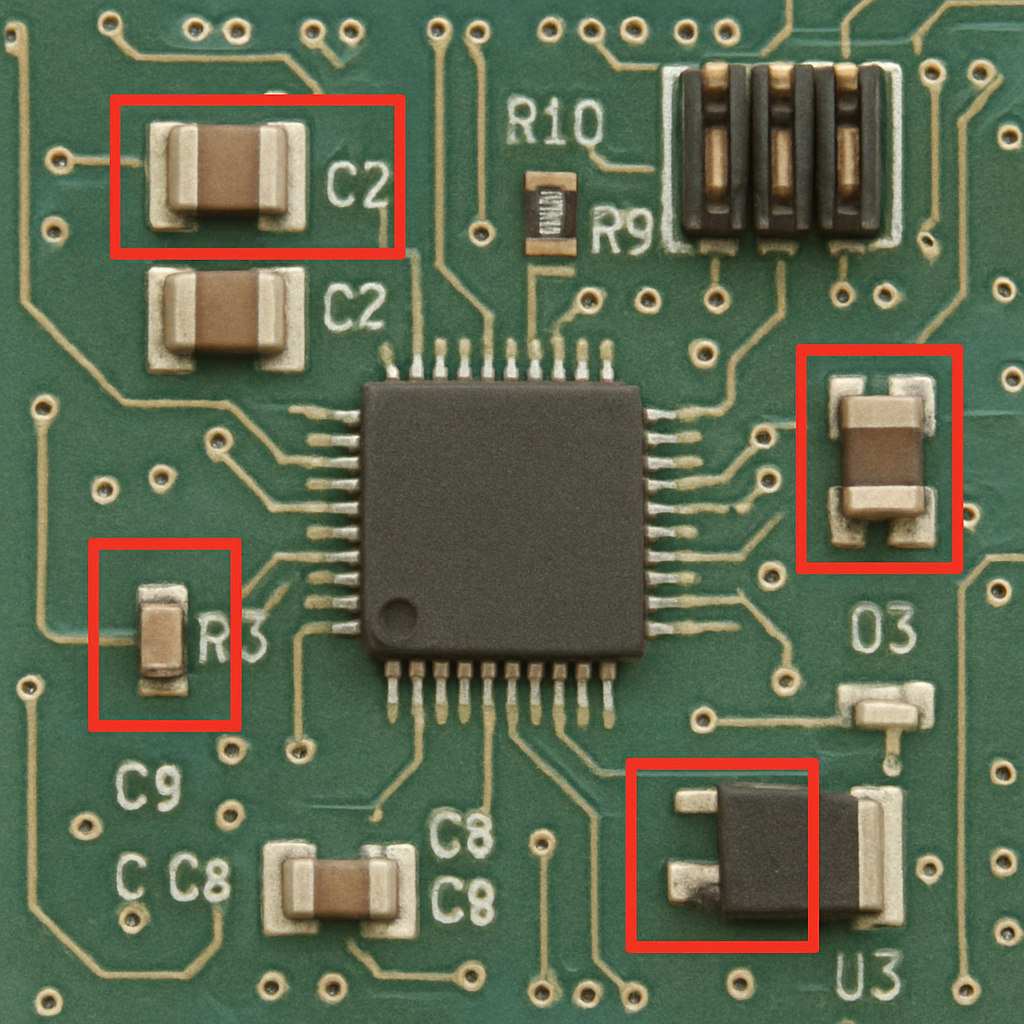
IPC 6011 vs IPC 6012: Key Differences and When to Use Each
IPC 6011 and IPC 6012 are both vital for PCB manufacturing. However, they serve different purposes and address distinct aspects of PCB quality and design.
IPC 6011 provides a broad framework for PCB quality. It covers varying types of PCBs and general requirements. This standard is more comprehensive in its approach to encompassing all PCB classifications.
On the other hand, IPC 6012 specifically targets rigid PCBs. It goes into much more detail for these types of boards. The guidelines include material specifications and specific testing methods unique to rigid PCBs.
Key differences between IPC 6011 and IPC 6012 include:
- Scope: IPC 6011 is broad, while IPC 6012 focuses on rigid PCBs.
- Detail Level: IPC 6011 offers general requirements; IPC 6012 is detailed.
- Application: IPC 6011 is versatile, IPC 6012 suits rigid PCBs.
Knowing when to use each standard is crucial. IPC 6011 is suitable when dealing with multiple types of PCBs. It supports diverse applications with general specifications.
For projects involving only rigid PCBs, IPC 6012 is more appropriate. Its in-depth focus ensures superior attention to the specific needs of rigid board manufacturing.
This distinction helps manufacturers and designers choose standards that match their project’s scope and requirements.
Understanding both standards allows for informed decision-making to achieve desired performance levels. This ensures compliance and quality in PCB production.
A visual comparison of IPC 6011 and IPC 6012 could be as follows:
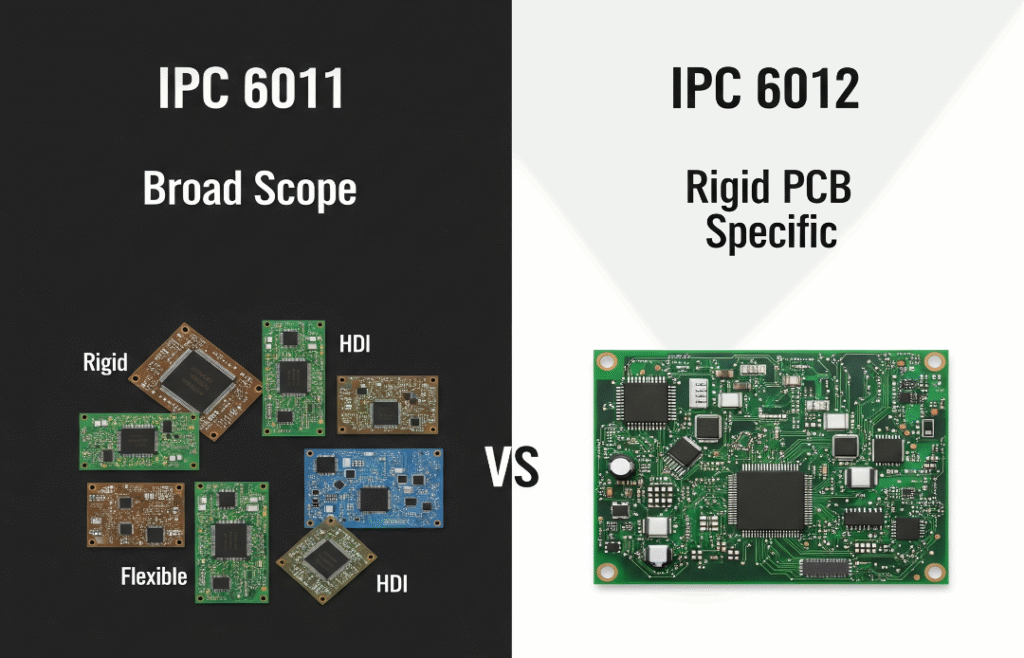
How IPC 6011 Impacts Design, Material Selection, and Quality Assurance?
IPC 6011 plays a crucial role in the design of printed circuit boards. It sets the framework for ensuring that PCBs meet industry standards for quality and performance. Designers rely on IPC 6011 to align their projects with these expectations from the start.
Material selection is directly influenced by IPC 6011 guidelines. The standard outlines acceptable materials based on performance requirements. This ensures that selected materials contribute to the board’s durability and efficiency.
Quality assurance benefits significantly from IPC 6011. The standard mandates comprehensive testing to verify a PCB’s functionality. This testing covers visual inspection, electrical testing, and environmental assessments, all crucial for reliable products.
Key aspects impacted by IPC 6011 include:
- Design: Ensures standards are met from the project outset.
- Materials: Influences selection for performance compatibility.
- Testing: Calls for rigorous quality checks to maintain reliability.
For PCB manufacturers, adherence to IPC 6011 equates to fewer defects and improved product longevity. This compliance not only strengthens product quality but also boosts customer satisfaction and trust.
The IPC 6011 standard is an invaluable tool in the electronics industry. By guiding design, material choices, and quality processes, it solidifies the production of high-grade PCBs. Ultimately, it ensures consistent delivery of reliable and innovative electronic solutions.
Industries and Applications Affected by IPC 6011
IPC 6011 impacts a broad array of industries. Its guidelines help maintain high quality across various applications, ensuring reliability and safety. This standard is pivotal in sectors that heavily depend on electronics.
Consumer electronics greatly benefit from IPC 6011. Devices like smartphones and tablets require consistent performance and durability. This standard aids manufacturers in achieving that by providing a clear quality framework.
In the automotive industry, IPC 6011 ensures that PCBs withstand harsh environments. Cars use numerous electronic components for vital functions, and this standard guarantees their reliability and safety. It is crucial for sustaining modern vehicle technology.
The aviation and aerospace sectors also rely on IPC 6011 for their critical systems. Here, PCBs demand unparalleled reliability due to the high stakes involved. The guidelines help reduce risks and assure performance in extreme conditions.
Key industries utilizing IPC 6011 include:
- Consumer Electronics: Smartphones, tablets, and gadgets
- Automotive: Electronics for safety and functionality
- Aerospace: High-reliability systems for aircraft
IPC 6011’s presence in these industries underscores its significance. By promoting superior quality, it empowers diverse applications, ensuring technological advancements meet modern standards.
Who is Responsible for IPC 6011 Compliance?
Compliance with IPC 6011 involves a joint effort across various roles. Each participant in the electronics manufacturing chain has specific responsibilities to ensure adherence to the standard.
Manufacturers carry a significant share of compliance responsibilities. They must integrate IPC 6011 guidelines into their production processes. This involves everything from material selection to final product testing.
Designers play a crucial role as well. They need to consider IPC 6011 standards during the PCB design phase. By understanding the standard’s requirements, designers can make informed choices that contribute to overall compliance.
Quality assurance teams are the gatekeepers of compliance. They perform the necessary inspections and tests that validate adherence to the standard. This requires a thorough understanding of the quality and performance criteria outlined in IPC 6011.
Entities involved in IPC 6011 compliance include:
- Manufacturers: Integrate standards in production
- Designers: Implement guidelines in the design phase
- Quality Assurance Teams: Ensure adherence through testing and inspections
Each party collaborates to uphold the standard. Together, they ensure that electronic products meet the high expectations set by IPC 6011.
Updates, Revisions, and the Evolution of IPC 6011
The IPC 6011 standard is not static but evolves with industry needs. Revisions are crucial to keep the standard relevant amid technological advances.
IPC continuously updates its standards, including IPC 6011. These revisions ensure the guidelines reflect current manufacturing techniques and materials. The updates aim to enhance quality and performance criteria for PCBs.
Regular revision cycles incorporate feedback from industry experts and stakeholders. This collaborative approach ensures the standard meets diverse industry requirements. Moreover, it facilitates innovation by adapting to new technologies and processes.
Key aspects of IPC 6011’s evolution include:
- Incorporation of new materials: Aligning with cutting-edge composites
- Adoption of advanced testing methods: For improved reliability
- Updating performance criteria: Reflecting modern application demands
These changes emphasize IPC 6011’s commitment to quality and industry advancement. Staying updated with the latest revisions is vital for professionals involved in PCB manufacturing. This knowledge ensures compliance and contributes to the production of reliable, high-quality electronic products.
Benefits of Adhering to IPC 6011 Standards
Compliance with IPC 6011 standards offers several advantages. It is vital in ensuring the integrity of PCBs. This standard helps manufacturers produce high-quality products, fostering customer satisfaction.
Adhering to these guidelines minimizes defects in electronic components. It results in more reliable and durable products. Reduced defects mean fewer recalls and less rework, significantly lowering costs.
IPC 6011 is recognized globally, enhancing market competitiveness. Products that meet these standards can confidently enter international markets. Furthermore, it aligns manufacturing with global expectations, aiding in regulatory compliance.
Some key benefits include:
- Improved product quality: Ensuring consistent manufacturing processes
- Cost savings: By reducing waste and rework
- Enhanced reputation: Through compliance and reliability
- Market expansion: Access to international clientele
IPC 6011 also supports innovation in design and manufacturing. Its guidelines help introduce new technologies with reliability. By adhering to IPC 6011, companies can maintain a competitive edge while ensuring the safety and dependability of their electronic products.
Conclusion
Grasping the essentials of IPC 6011 is crucial in electronics. It ensures that printed circuit boards meet high-quality standards. This consistency is vital for reliable and durable products.
For businesses, understanding these guidelines can enhance competitiveness. It opens doors to international markets through compliance. Following these standards not only boosts product quality but also drives innovation.