Surface Mount Technology (SMT) and Through Hole Technology (THT) are two key methods in electronic assembly. Each has unique features and benefits.
SMT involves placing components directly onto the surface of a printed circuit board (PCB). This allows for compact and efficient designs.
In contrast, THT requires inserting component leads through holes in the PCB. This method provides strong mechanical bonds.
Choosing between these techniques depends on various factors. These include production volume, component size, and application requirements.
SMT is often favored for high-volume production due to its automation capabilities. It helps make smaller and more compact designs.
THT, however, is preferred for applications needing durability and easy maintenance. It is ideal for components that face mechanical stress.
Understanding the differences between SMT and THT is crucial. It helps in making informed decisions for electronic projects.
This article will look at these techniques closely. It will compare their pros and cons.
Understanding Surface Mount Technology (SMT)
Surface Mount Technology (SMT) changes how we put together electronic devices. It allows us to place components on the surface of a printed circuit board (PCB). This technique eliminates the need for drilled holes, allowing more compact and sophisticated designs.
SMT is known for supporting a higher component density. It allows the placement of more components on a smaller area. This results in more intricate and complex circuitry, crucial for modern devices.
The SMT process typically involves several automated steps. First, solder paste is applied to the PCB pads. Next, pick-and-place machines position the components with precision. Finally, a reflow oven melts the solder paste, bonding the components to the board.
Notable benefits of SMT include automation efficiency and space optimization. As a result, it is favored in high-volume production scenarios and industries like telecom and consumer electronics.
Here are some key aspects of SMT:
- Supports higher component density
- Ideal for miniaturized devices
- Allows double-sided PCB assembly
Despite its advantages, SMT requires precise equipment for placement and soldering. The automation offers faster production, yet it demands careful setup and maintenance.
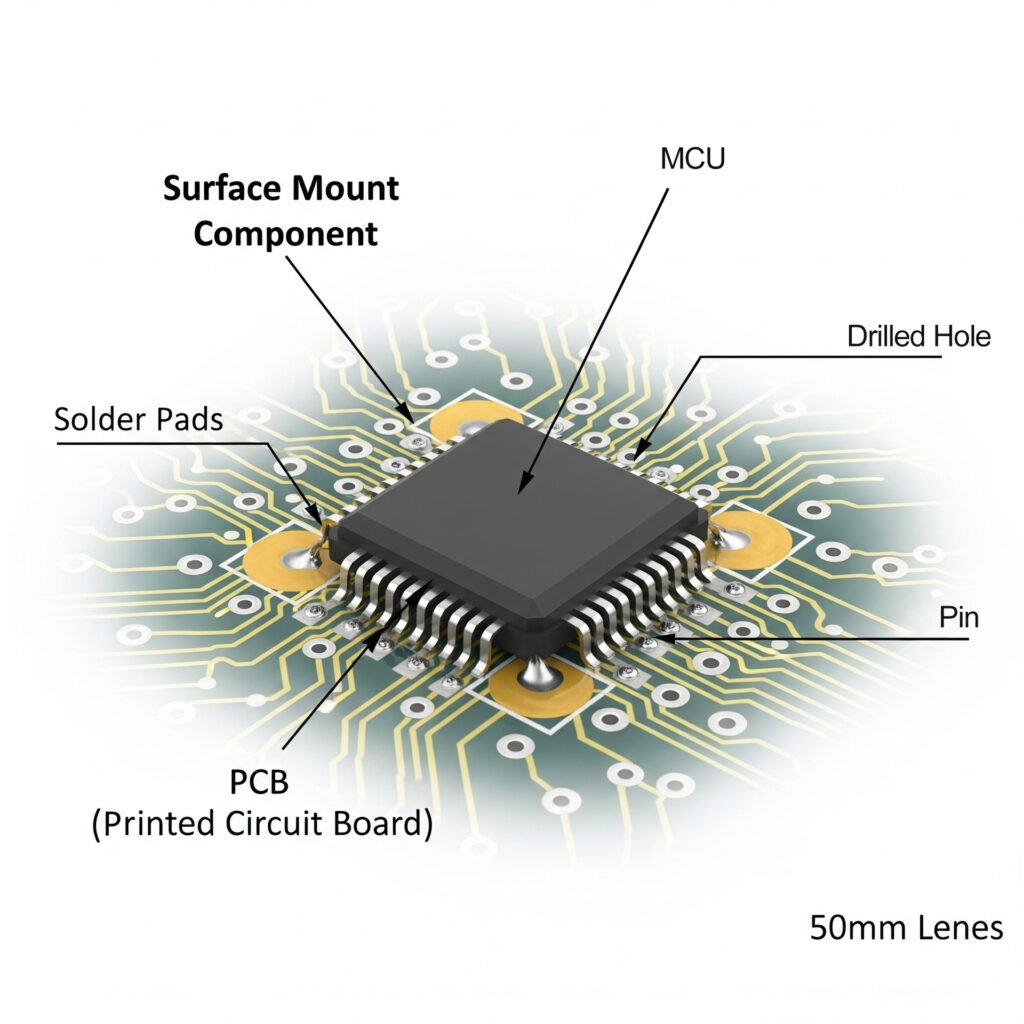
Understanding Through Hole Technology (THT)
Through Hole Technology (THT) is a classic method of electronic assembly. It involves inserting component leads into drilled holes on the PCB. These leads are then soldered to the board on the opposite side. This process creates a strong mechanical bond.
THT is known for its reliable solder joints. This makes it the go-to choice for components exposed to physical stress. It’s common in industrial applications where durability is crucial.
Compared to SMT, THT often results in larger circuit boards. Since components pass through the board, spatial requirements can lead to a bulkier design. This size can limit its use in miniaturized devices.
One of THT’s main advantages is its ease of manual assembly. This makes it suitable for prototyping and small production runs. Hobbyists and educational settings often prefer it for teaching electronics skills.
Key features of THT include:
- Strong mechanical connections
- Ideal for high-stress environments
- Simple manual assembly
While THT may not match SMT in automation, it excels in situations needing robust, easily maintainable connections. Manual soldering is simple and helpful, especially for regular repairs.
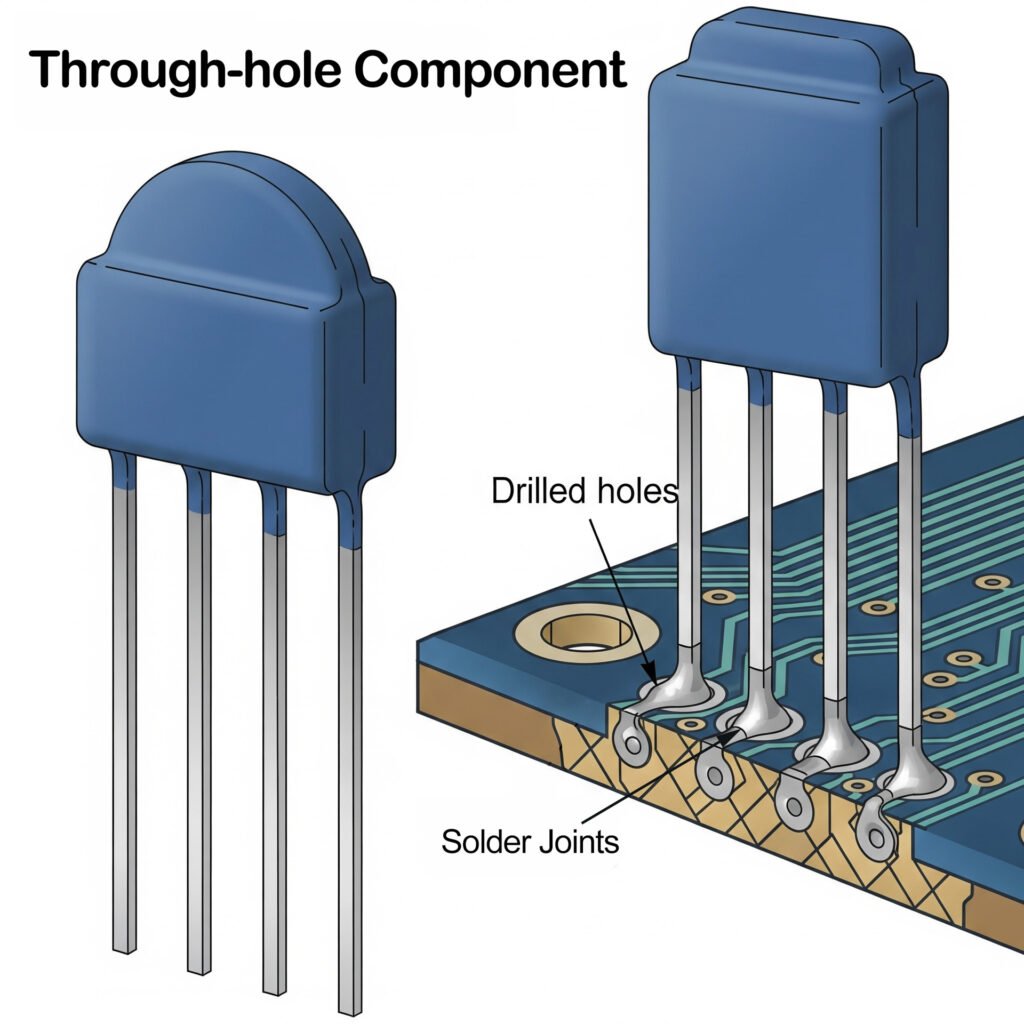
Key Differences: Surface Mount Vs Through Hole
Surface Mount Technology (SMT) and Through Hole Technology (THT) have distinct characteristics. These differences are crucial when selecting a technique for electronic assembly projects.

Characteristic | SMT | THT |
---|---|---|
Component Mounting | Components mounted directly on PCB surface | Component leads inserted through drilled holes on PCB |
Space Utilization | High, supports higher component density, compact designs | Lower, requires drilled holes, resulting in relatively larger board size |
Automation Level | Highly automated, fast production speed | Mostly relies on manual assembly/soldering, relatively slower production speed |
Production Cost | Lower cost for high-volume production | Lower cost for small-batch production and prototyping; higher cost for high-volume production |
Mechanical Strength | Relatively lower (primarily relies on pad adhesion) | Higher (leads pass through board and are soldered, providing strong mechanical connection) |
Heat Dissipation | Poorer (smaller component-to-board contact area, requires extra measures for heat dissipation) | Better (leads passing through the board provide additional heat dissipation paths) |
High-Frequency Performance | Excellent (low parasitic inductance and capacitance, suitable for high-frequency applications) | Relatively poorer (larger parasitic effects, limited high-frequency performance) |
Rework Difficulty | Higher (requires specialized equipment and techniques) | Lower (relatively easy for manual rework) |
Application Scenarios | Consumer electronics, smartphones, computers, and other miniaturized, high-density products | Industrial equipment, power supplies, military equipment, applications requiring highly robust connections |
Advantages of Surface Mount Technology
Surface Mount Technology offers numerous benefits that make it a popular choice in electronics. Its ability to accommodate high-density components is a key advantage. This feature is crucial in modern devices where space is at a premium.
Additionally, SMT supports smaller and lighter components compared to THT. This results in the production of sleek, compact electronic devices. Technology is very important in industries that focus on making things smaller, like telecom and consumer electronics.
SMT also enhances production efficiency. The automated assembly process reduces time and labor costs, particularly in large-scale manufacturing. This automation leads to quicker turnaround times, aiding in rapid market deployment.
Finally, Surface Mount Technology provides good signal quality and less electrical noise. These benefits improve device performance significantly. SMT contributes to the creation of sophisticated electronic systems with fewer design limitations.
In summary, the advantages of SMT include:
- High-Density Component Placement
- Smaller, Lighter Components
- Automated and Efficient Production
- Enhanced Signal Integrity and Reduced EMI
Drawbacks of Surface Mount Technology
Surface Mount Technology, while advantageous, has its drawbacks. One major challenge is the requirement for precise equipment and techniques. Specialized machinery and expertise are necessary, which can increase initial setup costs.
Additionally, SMT components are often more prone to thermal and mechanical stress. During reflow soldering, these components can suffer damage, impacting the overall reliability of the electronic device.
Repairing and replacing components on SMT boards can also be difficult. The dense placement and small size of components can complicate maintenance and prolong repair times. This makes servicing these devices more challenging than with Through Hole Technology.
Lastly, SMT components can be more sensitive to electrostatic discharge (ESD). This sensitivity requires careful handling and specific precautions during assembly and operation.
In summary, the downsides of SMT are:
- High Initial Setup Costs
- Sensitivity to Heat and Pressure
- Complex Repair Processes
- Increased Sensitivity to ESD
Advantages of Through Hole Technology
Through Hole Technology (THT) offers several notable benefits, making it a preferred choice in specific scenarios. One of its primary advantages is the robust mechanical bond it provides. This is particularly beneficial for components that endure physical stress or require strong anchoring.
Furthermore, THT components are generally easier to handle and assemble manually. This makes THT especially suitable for prototyping, low-volume production, and educational purposes. The larger size and straightforward design of THT components facilitate manual soldering, inspection, and testing processes.
In addition, THT components excel in thermal management. The through-hole mounting method helps to spread heat. This is important for power parts and uses that get very hot.
This characteristic makes THT appropriate for power circuitry and high-temperature environments.
Lastly, THT’s straightforward design allows for easy replacement and repair. In situations where it is important for parts to be easy to use, THT provides a helpful solution.
The advantages of Through Hole Technology include:
- Strong Mechanical Bonds
- Ease of Manual Assembly
- Enhanced Thermal Management
- Simplified Component Replacement
Drawbacks of Through Hole Technology
Despite its advantages, Through Hole Technology (THT) has several limitations. One significant drawback is the increased PCB size due to the necessary drilled holes. This leads to bigger and sometimes heavier PCBs. This can be a problem for devices that need to be smaller.
Additionally, THT is less suited for automation, leading to higher labor costs in large-scale production. The manual assembly process can be time-consuming, contributing to longer production cycles.
THT components usually occupy more space and restrict design flexibility. This can limit the complexity and integration levels achievable in electronic designs.
Moreover, THT may struggle to meet the demands of high-frequency applications. The extended lead lengths can introduce unwanted electrical noise and compromise signal integrity.
Challenges associated with Through Hole Technology include:
- Larger PCB Size and Weight
- Higher Labor Costs
- Limited Design Flexibility
- Potential Signal Integrity Issues
Process Comparison: Assembly, Soldering, and Inspection
When comparing assembly processes, Surface Mount Technology (SMT) offers high levels of automation. Machines place components swiftly, resulting in rapid production cycles. This automation helps reduce human error, enhancing overall consistency and quality.
Conversely, Through Hole Technology (THT) often relies on manual assembly. Individuals insert component leads through pre-drilled holes, requiring precision and skill. This manual approach can extend production time and increase labor costs.
Soldering techniques also differ between the two technologies. SMT uses reflow soldering, where solder paste is melted in a controlled oven environment. This ensures uniform solder joints across the board. THT often employs wave soldering, where boards pass over a wave of molten solder, bonding the leads to the PCB.
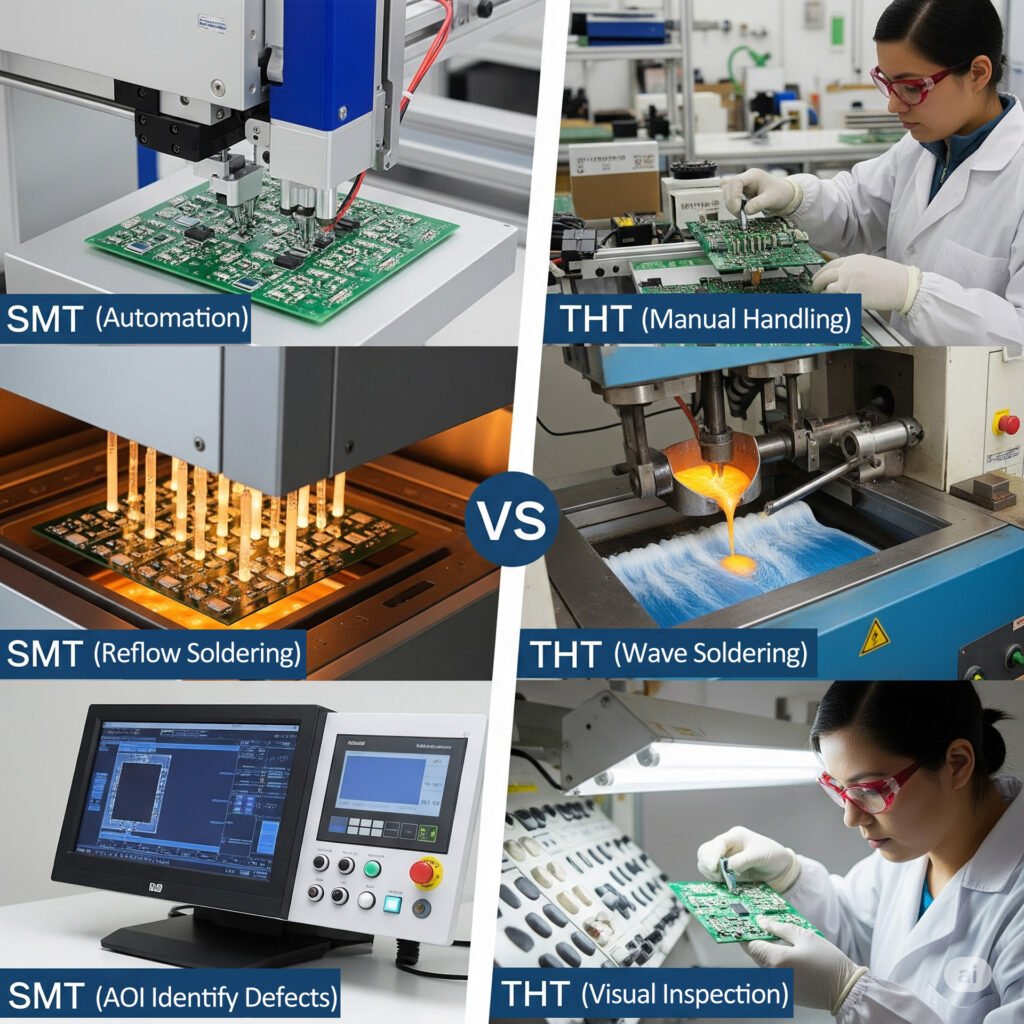
Inspection processes highlight another contrast. SMT frequently utilizes automated optical inspection (AOI) systems. These systems rapidly detect and correct assembly errors. In THT, visual inspection remains a common practice, requiring skilled technicians for accurate assessment.
Key distinctions in the process include:
- Assembly: Automation vs. Manual Handling
- Soldering: Reflow vs. Wave Soldering
- Inspection: Automated vs. Visual
Considerations for Choosing SMT & THT
Deciding between Surface Mount Technology (SMT) and Through Hole Technology (THT) is often not binary. Many projects benefit from combining both methods. Each technique offers unique benefits that can be leveraged within the same project.
Cost Differences
Cost considerations are crucial when choosing between Surface Mount Technology (SMT) and Through Hole Technology (THT). Each technique presents unique cost implications that affect overall production budgets.
SMT generally reduces labor costs due to its high level of automation. Automated processes lead to faster assembly times and decreased human intervention. This results in a more streamlined, cost-effective production cycle for large volumes.
In contrast, THT often incurs higher labor costs. The manual assembly nature of THT requires more workforce involvement. This increases expenses, especially for small- to medium-scale productions where automation is less feasible.
Material costs also vary between the technologies. SMT employs smaller components, leading to lower material costs. THT components, being larger, often demand more raw materials and additional soldering supplies.
In summary, consider these points:
- Labor Costs: Higher for THT due to manual processes.
- Material Costs: SMT components are generally less expensive.
- Automation Savings: SMT benefits from automated efficiency.
Application-Specific
Choosing between Surface Mount Technology (SMT) and Through Hole Technology (THT) depends on the specific requirements of each application. Each technique offers distinct advantages that make them suitable for various scenarios.
SMT is great for making small electronic devices. It’s frequently used in smartphones and tablets, where space and weight are paramount. The ability to place components on both sides of a PCB enhances design flexibility for complex circuits.
In applications subject to mechanical stress, THT is the preferred choice. Its strong physical connections are beneficial in environments like aerospace and industrial settings, where robustness is critical. THT components also facilitate easier maintenance and replacement when necessary.
Deciding factors include the environment in which the electronic device operates and the need for future upgrades or repairs.
Consider these additional points:
- High-frequency applications: SMT is advantageous.
- Durability: THT excels in vibration-intense environments.
- Maintenance: THT allows easier component swaps.
production volume & design requirements
SMT is typically used when space and weight reductions are crucial. It supports high-volume production efficiently due to automation. On the other hand, THT is optimal for components requiring robust mechanical attachments.
In mixed-technology assemblies, SMT can manage passive and smaller components, while THT handles connectors and power components. This hybrid approach enhances both performance and reliability, suiting diverse design requirements.
Scenarios to Consider:
- Use SMT: When size constraints are critical.
- Use THT: For components under mechanical stress.
- Use Both: When a balance of space and durability is needed.
Future Trends in PCB Assembly Techniques
As technology progresses, PCB assembly techniques continue to evolve. Innovations like 3D printing and flexible PCBs are becoming more prominent. These advancements allow for enhanced design possibilities and increased functionality in compact spaces.
Moreover, the integration of Artificial Intelligence (AI) in manufacturing promises greater precision and efficiency. AI-driven automation can optimize component placement and ensure quality control. The future has many exciting possibilities. We will see better, quicker, and more efficient ways to assemble PCBs.
Conclusion
Selecting the right PCB assembly method depends on your project’s specific needs. Consider factors like production volume, cost constraints, and technical requirements. Surface mount technology suits compact, high-speed applications, while through hole is better for durability and strength.
Evaluate each project’s unique demands to determine the best choice. It’s vital to balance functionality, cost, and design complexity. With a thorough understanding of both techniques, you can make informed decisions that best meet your electronic assembly goals.