In the intricate world of printed circuit board (PCB) manufacturing, precision and quality are paramount. One critical aspect that significantly impacts the performance, durability, and aesthetics of PCBs is edge beveling. A beveler is a specialized tool designed to create angled edges on PCBs, which can serve various functional and aesthetic purposes. This article will provide a comprehensive guide to mastering PCB beveling, covering the techniques, tools, and best practices involved in this essential process.
What is a Beveler?
A beveler is a precision tool designed to cut or grind a specific angle on the edge of a PCB. The term “bevel” refers to an angled surface that is not perpendicular to the main surface of the material. In PCB manufacturing, beveling is typically performed on the edges of the board to achieve a desired slope or angle. This process can enhance the aesthetics of the PCB, improve mechanical strength, and facilitate assembly processes.
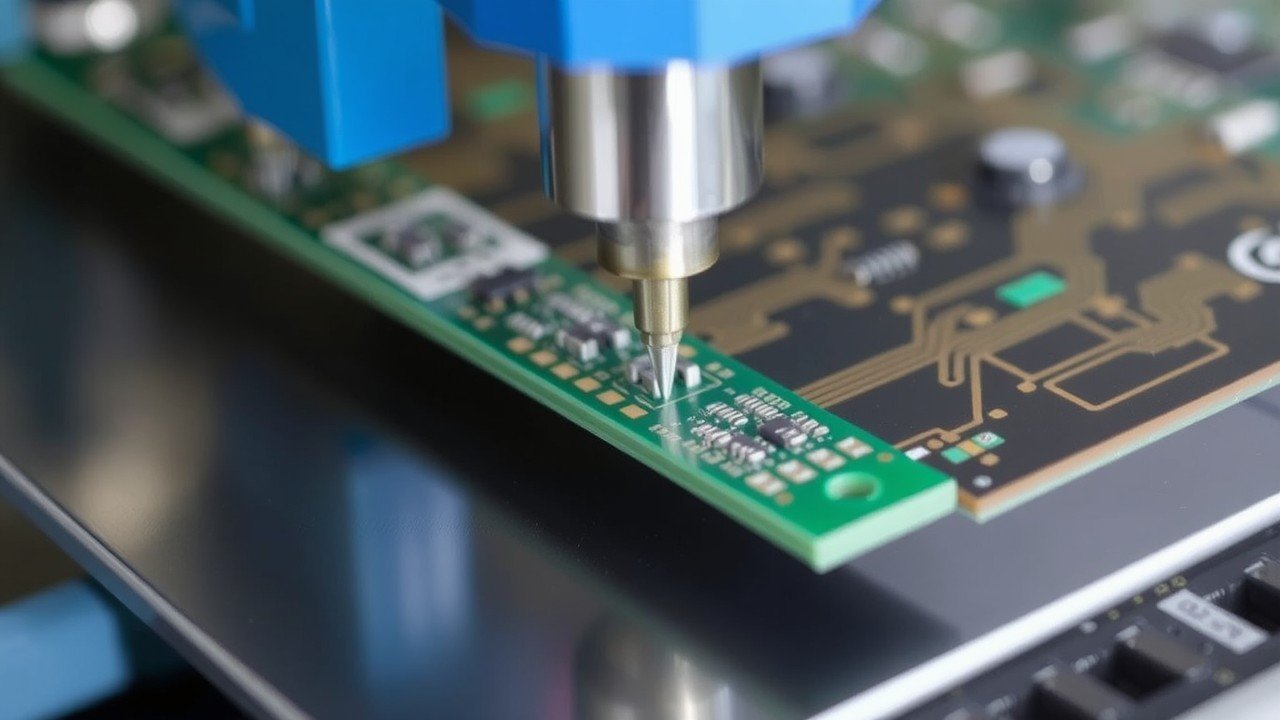
Required Materials and Components for Beveling:
- PCB Substrates: Common materials include FR-4 (glass epoxy), Rogers, and flexible substrates like polyimide.
- Beveling Tools: These can be diamond-coated grinding wheels, carbide cutters, or abrasive belts.
- Fixtures and Clamps: Used to hold the PCB securely during the beveling process.
- Cooling Systems: Often necessary to prevent overheating, which can damage the PCB.
Techniques for Effective Beveling
Manual Beveling
- Operation: Handheld tools where the operator controls the angle and pressure.
- Tools: Files, sandpaper, and manual grinders.
- Applications: Suitable for small-scale production, prototyping, and custom jobs.
Automated Beveling
- Operation: Computer Numerical Control (CNC) machines that follow pre-programmed instructions.
- Tools: CNC routers, laser cutters, and robotic arms.
- Applications: Large-scale production, high-precision requirements.
Hybrid Beveling
- Operation: Combines manual and automated features, allowing for some operator control while maintaining precision.
- Tools: Adjustable CNC machines with manual overrides.
- Applications: Mid-sized operations, projects requiring both flexibility and accuracy.
Beveling Process
Beveling is the process of creating an angled edge on a PCB. This is achieved by removing material from the edge to form a sloped surface.

The beveling process generally involves the following steps:
Preparation: The PCB is prepared for beveling, which may include cleaning and inspection to ensure it is free of defects or contaminants.
Loading: The PCB is loaded into the beveler, either manually or through an automated feeding system.
Programming: If using a CNC beveler, the machine is programmed with the desired angle, depth, and speed parameters.
Beveling: The machine applies the cutting tool to the edge of the PCB, removing material to form the specified angle.
Inspection: After beveling, the PCB undergoes inspection to verify that the edge meets the required specifications.
Post-Processing: Depending on the application, additional steps such as edge coating or finishing may be necessary to protect the newly beveled edge.
Best Practices for Effective Beveling
Material Inspection
- Pre-Beveling: Inspect the PCB for defects, warping, or surface imperfections.
- Post-Beveling: Verify that the bevel meets the required specifications.
Clamping and Fixturing
- Pre-Beveling: Inspect the PCB for defects, warping, or surface imperfections.
- Post-Beveling: Verify that the bevel meets the required specifications.
- Secure Holding: Use fixtures and clamps to hold the PCB firmly in place.
- Alignment: Ensure the PCB is properly aligned to achieve a consistent bevel.
Angle Setting
- Precision: Use a protractor or CNC programming to set the desired angle accurately.
- Verification: Double-check the angle before starting the beveling process.
Feeding the Board
- Controlled Rate: Feed the PCB through the tool at a controlled rate to ensure uniformity.
- Speed Adjustment: Adjust the feeding speed based on the material and tool being used.
Post-Processing
- Inspection: Thoroughly inspect the beveled edge for any defects or inconsistencies.
- Finishing: Polish or coat the beveled edge to enhance appearance and durability.
Applications of Bevelers in PCB Manufacturing
Edge Preparation for Assembly
- Soldering and Component Placement:
Beveled edges can help in the soldering process by providing a smooth transition between the board and the components. This reduces the risk of solder bridging and improves the overall reliability of the connections.
- Edge Connectors:
For PCBs that use edge connectors, beveling the edges ensures a better fit and more reliable electrical contact. The beveled edge allows for easier insertion and removal of the connector, reducing wear and tear over time.
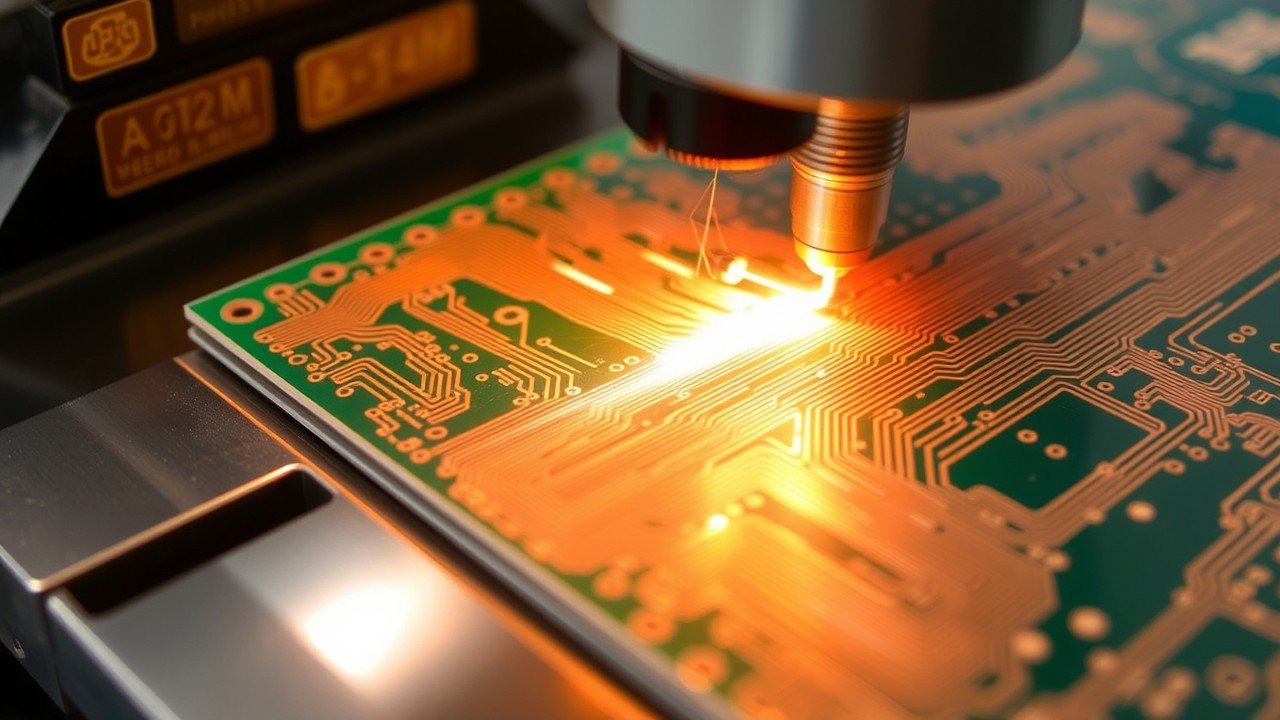
Mechanical Strength and Durability
- Stress Relief:
Beveling the edges of a PCB can reduce stress concentrations at the corners, which are often the weakest points. By creating a smoother transition, the board becomes more resistant to cracking and breaking during handling and installation.
- Edge Protection:
Beveled edges can also protect the board from chipping and damage, especially during transportation and storage. This is particularly important for high-reliability applications where even minor damage can lead to failure.
Aesthetic Enhancements
- Visual Appeal:
Beveled edges give the PCB a more professional and polished appearance. This is especially important for consumer products where the visual quality of the electronics can influence customer perception.
- Customization:
Bevelers can create a variety of angles and finishes, allowing manufacturers to customize the look of their PCBs to meet specific design requirements.
Conclusion
The beveler is a versatile and essential tool in PCB manufacturing, offering a range of benefits that enhance the performance, durability, and appearance of circuit boards. From protecting against mechanical damage to improving solderability and fit, the applications of bevelers are diverse and crucial to the success of many electronic products. As the demand for high-quality, reliable PCBs continues to grow, the role of the beveler in the manufacturing process will remain indispensable.